Zipp Engineer Interview Series
All About Carbon Fiber, Part III: How Zipp Makes Bicycle Wheels
This is the final episode of a three-part Zipp Speed Podcast series all about carbon fiber. Part I looked at the basic properties on carbon fiber and Part II on designing carbon wheels. Part III examines how Zipp manufactures its carbon fiber wheels.
In this final episode, Factory Engineering Manager Ruan Trouw provides an inside look at the Zipp factory in Indianapolis when it comes to manufacturing carbon-fiber rims. Ruan takes us through each step of the wheel-manufacturing process. Before his current role at SRAM Indianapolis and Zipp, Ruan was manufacturing engineer and was part of Zipp’s advanced development team. Please also listen to Part I of this season, All About Carbon Fiber, and Part II, Design Carbon Fiber Wheels. Below are edited excerpts from host Daniel Lee’s conversation with Ruan:
Where does the Zipp manufacturing process start, on the cut table?
It starts even a little before that when the carbon arrives here in Indy. When our carbon arrives, already frozen, a small temperature recorder travels with it. We analyze that data to make sure that the carbon has not sat out somewhere and heated up and lost some of its out-life. The way our carbon arrives, it’s in a B stage, the epoxy is already mixed. Any time it heats up we lose some of its workability time. We have to do some inspection.
Then what happens?
We go through a thawing process to make sure we don’t introduce any moisture into the laminate. Then we pull them out and we can start cutting shapes.

How does the carbon cut table work?
It’s basically a long routing table. You can either use a drag blade or a “pizza cutter.” The tables were originally designed to cut fabric. We use a cut table that is essentially a router that you can unroll a long sheet of material on and cut specific pieces and shapes. We do multistage cutting. We build tables of multiple layers of carbon and come back and cut that have a specific stack-up of layers.
How many pieces of carbon are in a Zipp wheel?
We could have over 30 pieces that need to be placed. Each one of those would consist of several layers with fibers in specific directions to give us the strength needed. These layers vary by model. When you start looking at higher performance, this tailoring of the laminate becomes more complex.
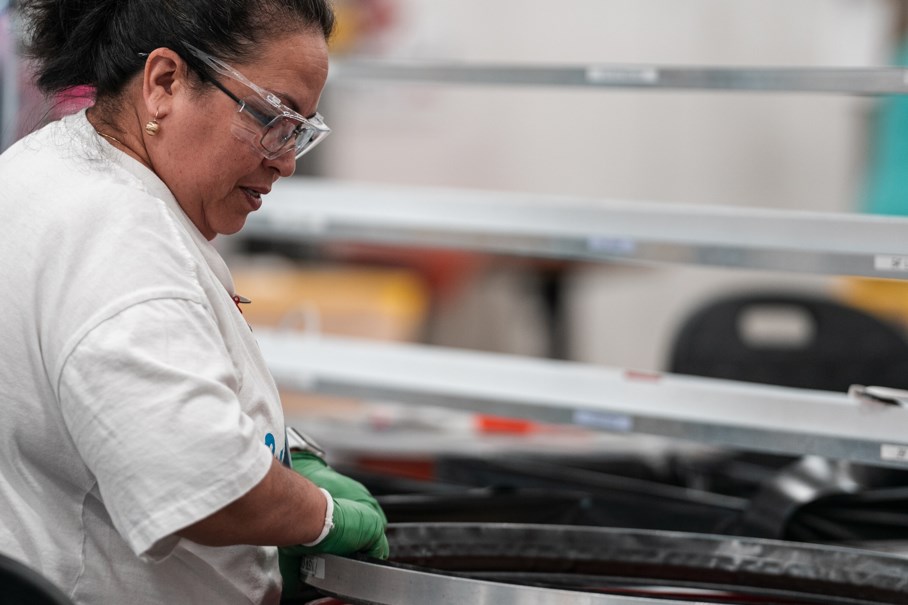
The more you care for a product, the easier it is to keep your quality high. It comes back to people, how you treat your people and how you embrace them and their viewpoints and inputs. Make life as easy as possible for them, and they will take care of the rest.
–Ruan Trouw, factory engineering manager
What happens in the wheel pre-form area?
Within our cells, we have several operators and break out the workload amongst them in order minimize the time spent on each of the steps. An operator manipulates the carbon to get to a preform that looks like a rim that is really to go into the press.
And the press is kind of like an oven?
The big thing with composites, especially when you work with pre-preg, is you need heat and pressure to get a good quality part at the end of the line. … We end up heating the carbon to a specific temperature for a specific ramp rate, and then supplying pressure when we need to get good consolidation. Then, once it’s cured it’s cooled down.
… There’s a lot that’s going on controlling the resin flow during the cycle. That flash (excess resin) needs to be cleaned up.
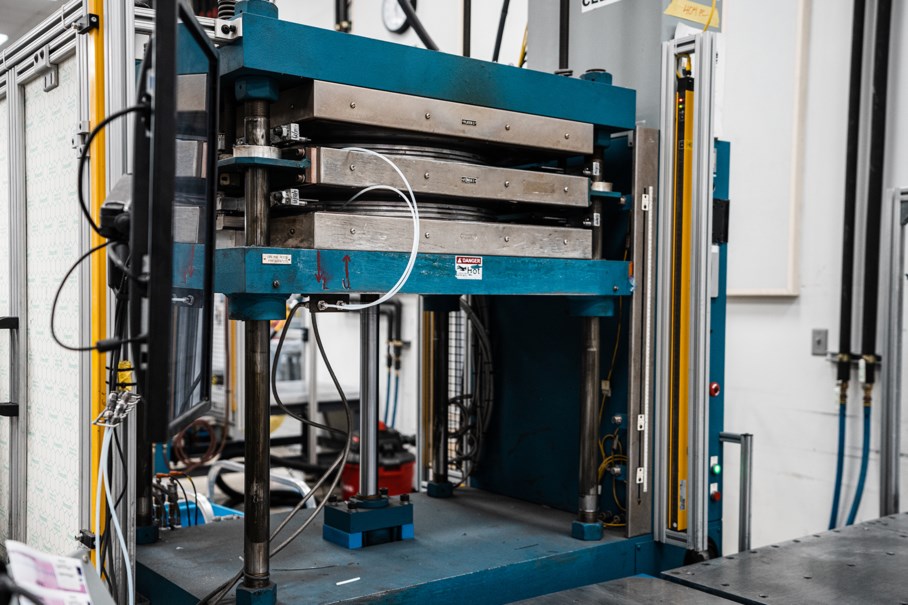
What’s next?
We start by drilling the valve hole. Then it will go in a drilling machine to drill for (spoke holes).
Is drilling something we’ve looked at very closely?
Drilling can seem simple. But when you’re working with this many holes at very specific angles, you start running into tool temperate issues, accuracy hole-to-hole, slip. We spend a good bit of time monitoring drills… so by the time it makes it into to wheel build we have a rim that performs the same every time.
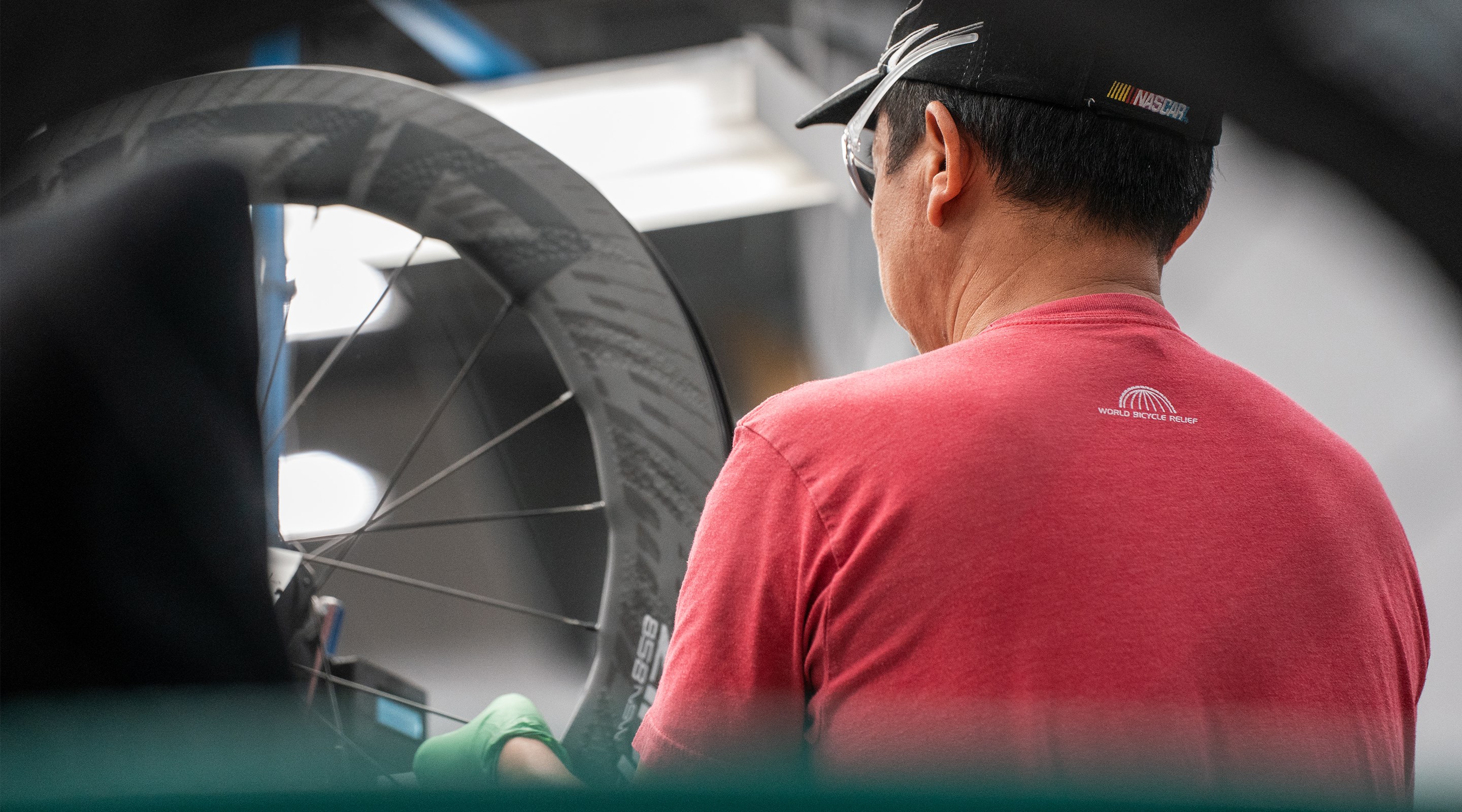
Now it goes to wheel building.
When you get to the point where performance means everything to the customer, we tailor the rim so much that you reach a point where the slightest changes in your build could change the performance of your wheel. A little too much spoke tension, you have one problem, too little spoke tension and you have another. We have to make sure that our builds are very accurate and that operators have everything they need to perform that build. Just about everything in our factory is run off the serial number that is on that rim. Not only can we see the whole history of the rim, but also, we use that for processing internally. The operator can scan that serial number and it will give them all fo the build specifications that they need for that specific rim.
That Zipp wheel then gets its distinctive graphics, is inspected, and finally boxed up and shipped to you. For much more detail on the Zipp process, please listen to the full episode.
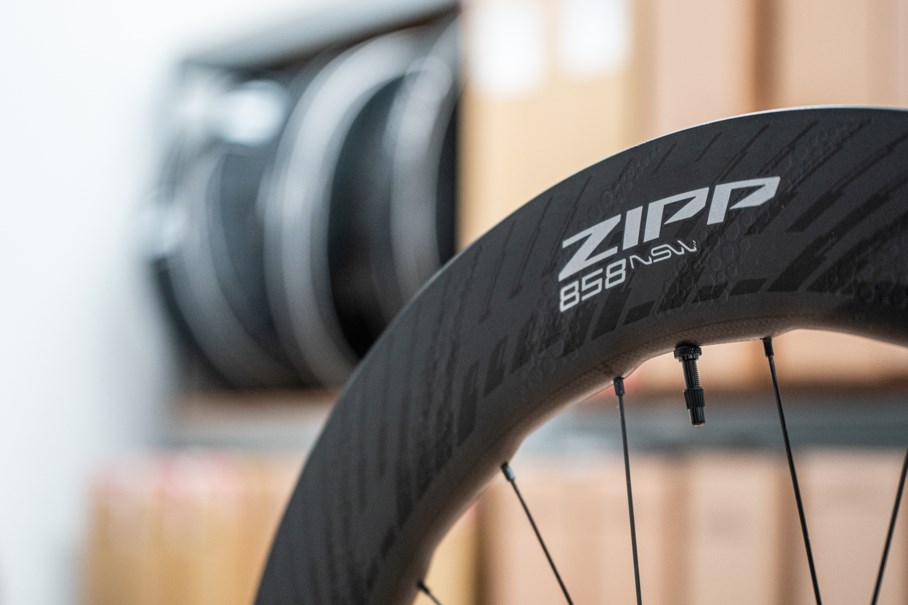